Friction and wear testing facility
Why DRIE-D developed this testing rig
Applications in the market are becoming larger, stronger and heavier which results in innovative designs. Validating these designs is of the utmost importance before commissioning large scale projects. One of the most widely used methods to validate designs is by testing.
DRIE-D is specialized in providing solutions for mechanical motion with both high friction and low friction materials. Each material behaves uniquely under different conditions, influenced by factors such as counterface material, surface roughness, temperature, load, and lubrication.
The variability in these factors makes it challenging to predict performance and understanding these complexities is crucial for optimizing material performance and ensuring reliability in various applications.
To support our customers in validating their designs. The testing rig’s advanced measurement and analysis capabilities enables our engineers to optimize designs for increased durability and efficiency.
At DRIE-D, we are driven by the challenge of your project-specific testing requirements. Our team is eager to explore the vast possibilities that our testing facilities has to offer for your applications and designs.
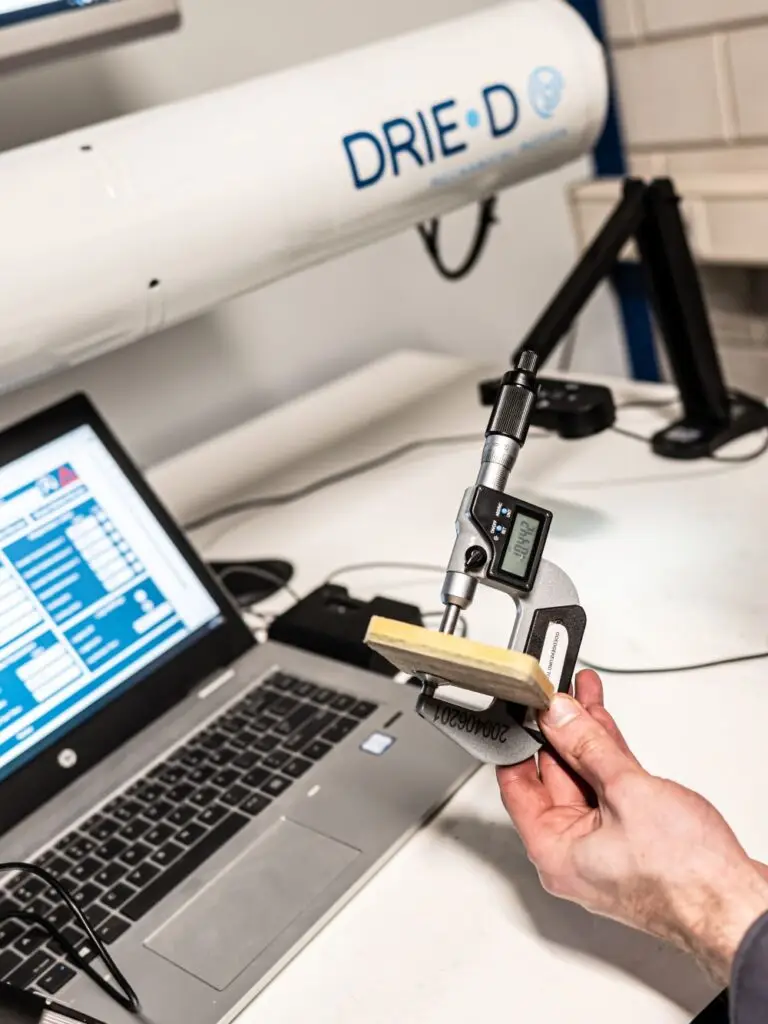
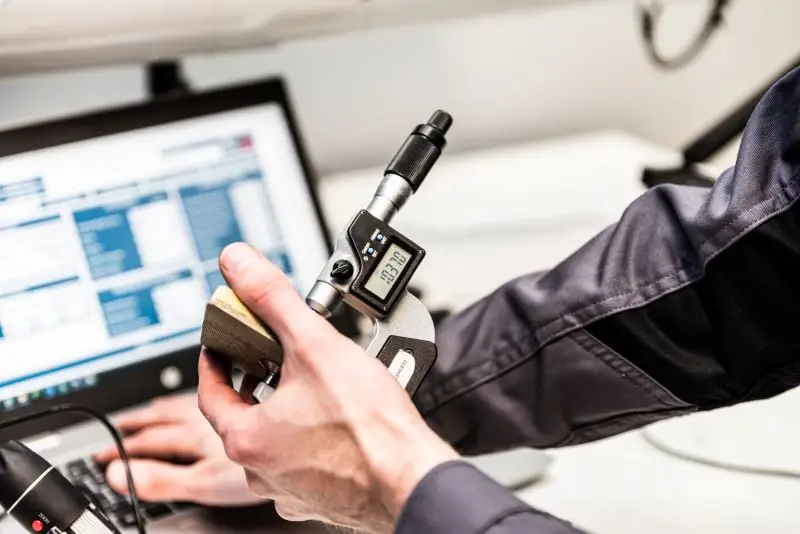
Test sliding behaviour of every possible material combination
In the testing facility we keep track of all variables to get a good understanding of the overall sliding behaviour of any material combination in any application. All aspect are monitored and measured. The outcome of the tests provide great insight that can be used for material selection and design improvements.
From tests in a clean environment with a perfectly machined counterface to a fully in (sea)water submerged condition with a corroded steel counterface, everything is possible.
Whether it is pushing the boundaries of existing materials or embarking on project-specific testing for our clients, DRIE-D’s test facility stand ready to transform challenges into achievements, ensuring your concepts reach their full potential.
Core elements test rig
- Test sample: Central to the rig’s functionality is a flat pad. This sample of the tested material is subjected to a controlled vertical load. The pad faces a counterface that is installed in a carrier that moves back and forth at a set velocity and stroke simulating the real-world application. Standard test sample dimensions are, at 50×50 mm or 75×75 mm, much larger than most standardized tests and we can accommodate a wide range of material types and sizes.
- Interchangeable counter surfaces: The carrier that supports the counterface plate boasts a user-friendly design that allows for the quick and easy replacement of the counterface material. This feature not only facilitates a broad spectrum of tests but also maintains cost-effectiveness by enabling repeated use across different experiments.
- Robust hydraulic system: The application of both vertical loads and horizontal movements is applied through powerful hydraulic cylinders, equipped with inline load cells and incorporated distance measurement sensors. This setup ensures precise control over the test parameters, enabling accurate assessments of material behavior under various conditions.
- Cooling: The counterface can be directly cooled through cooling channels in the carrier. Heat generated by friction can be dissipated during a test through the cooling liquid. This way tests can be performed faster and longer while mitigating the risk of overheating. The cooling temperature can be varied to the needs of the test.
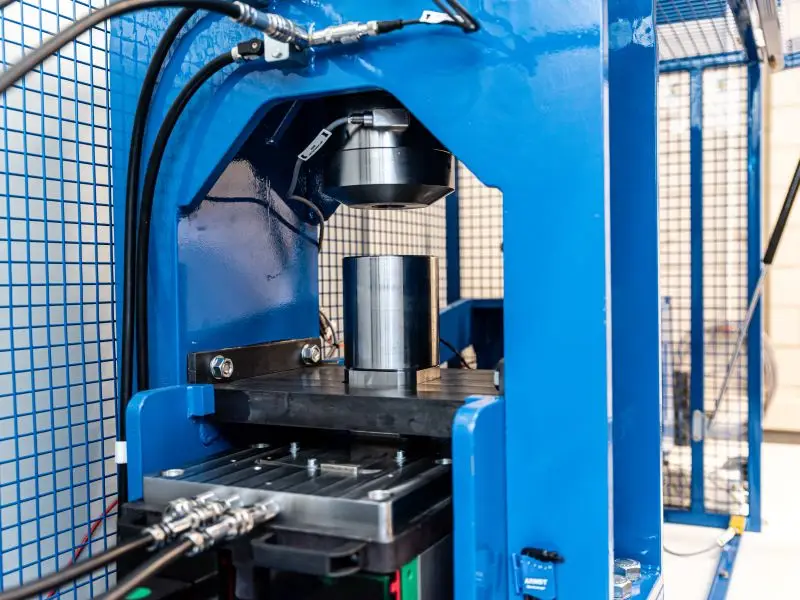
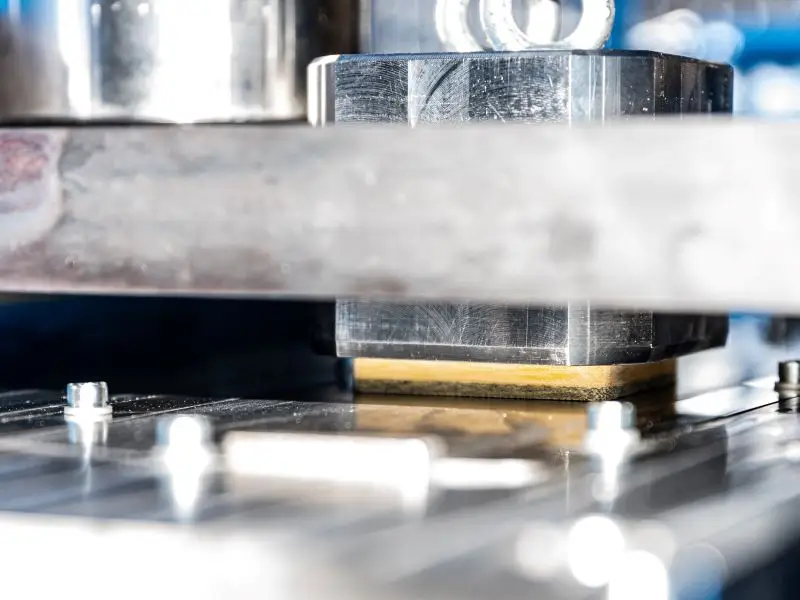
Possibilities test conditions
Sliding in clean and dry environments is easy, but D-glide® is often used in more demanding environments, such as with contamination or submerged in (sea)water. Our testing rig is equipped to perform tests in every possible condition. A watertight ring can be placed around the countersurface, which allows for testing with (sea)water, lubrication, contamination or a combination of these. If required, the (sea)water can even be circulated and filtered to simulate long-term use of D-glide® in the ocean.
- Environments:
- Dry and clean: Assessing performance without lubrication in a laboratory clean condition.
- Wet / water spray: Evaluating material behavior when exposed to water, such as in rain or in the splash zone aboard vessels.
- Submerged in (sea)water: Testing in fully submerged scenarios to mimic real-world aquatic (subsea) environments, with or without circulation and/or filtering.
- Optional:
- Contamination: Is all environments contamination can added to mimic the real-life application best as possible.
- Lubrication:
Understanding how different lubricants affect material pairing under various operating environments. - Cooling:
Controlling the environmental temperatures and enabling accelerated wear tests without overheating the material.
Data collection and analysis
- Contact pressure and load: All loads are measured inline by load cells for accurate control and assessment of the applied load and therefore contact pressure on the test sample.
- Temperature monitoring: The rig continuously monitors temperatures at all critical points, including the counter surface (in three locations), the sample’s back side and both the cooling inlet and outlet. This allows for a detailed understanding of thermal effects during testing and allows for safety measures to avoid overheating of the system.
- Wear and deformation tracking: A digital displacement sensor integrated in the vertical cylinder provides accurate measurements of material wear. This provides insight in the progression of wear rates over time and sliding distance. The durability of a design can thus be validated.
- Speed and position control: Another digital displacement sensor in the horizontal cylinder, meticulously records velocity and position of the carrier. This enables accurate positioning, velocity measurement and stroke setting.

Challenge us with your project specific testing requirements
At DRIE-D, we are driven by the challenge of your project-specific testing requirements. Our team is eager to explore the vast possibilities that our testing facilities has to offer for your applications and designs.
Whether you are in the early stages of material selection or looking for innovative ways to enhance your product’s performance, we can assist you and provide the insights and support you need. Contact our engineers at engineer@drie-d.com.