Grave Weir: Reliable water management through modern engineering
Regulating the water level to keep the Meuse navigable
The Grave Weir, located near the town of Grave, is a crucial part of the Dutch water management system, regulating water levels and ensuring safe navigation on the river Meuse. On behalf of the Ministry of Infrastructure and Water Management (Rijkswaterstaat) the contractor Combination Mourik Swarco (CMD) carried out maintenance on the Grave weir. For the replacement of the yokes, gates and drives, CMD requested to replace the parts with maintenance-friendly and more sustainable alternatives.
Proper working weir gate rollers are crucial for the opening and closing of the weir gates and DRIE-D was asked to develop and supply a maintenance-free bearing solution which fits within the existing dimensions. Each component is designed for this specific application, is maintenance-free and can withstand the demanding conditions of the weir environment.
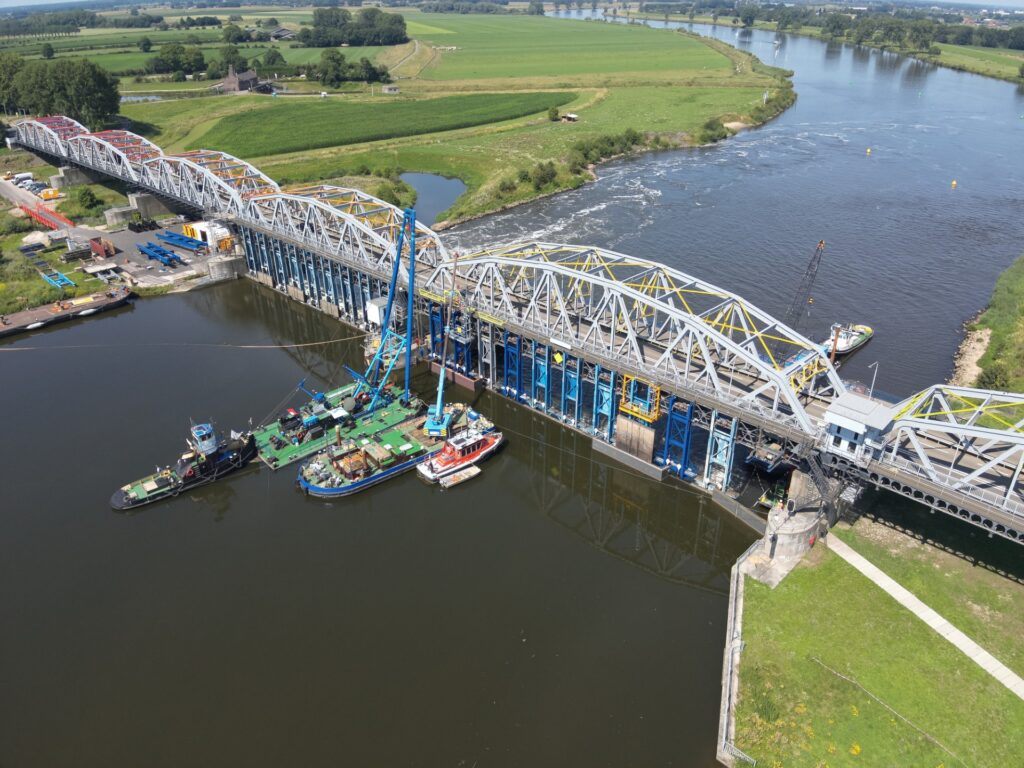
Project Grave weir, image: Rijkswaterstaat
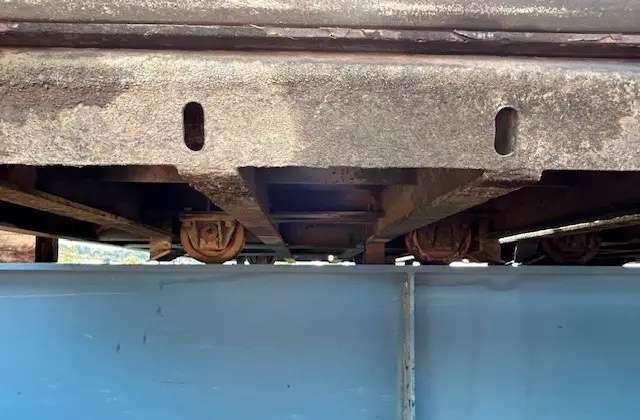
The challenge:
Designing a reliable and sustainable system in a limited time frame
Because the project was under great time pressure, urgency was required and a new and reliable bearing design had to be made within a short amount of time. It took only 5 weeks from the initial contact until the final design and after that the first batch of 24 roller assemblies were delivered within 8 weeks.
During the design phase we focused on solving the difficulties and problems with the original design. Maintenance, by means of manual lubrication, was necessary to keep the gate rollers running and to make the Grave weir function reliably. However, applying the lubrication was highly labour-intensive due to the difficult accessibility of the grease nipples.
By creating a maintenance-free design, these problems are eliminated and the system is no longer dependent on lubrication.
The solution:
A maintenance-free custom design with D-glide®
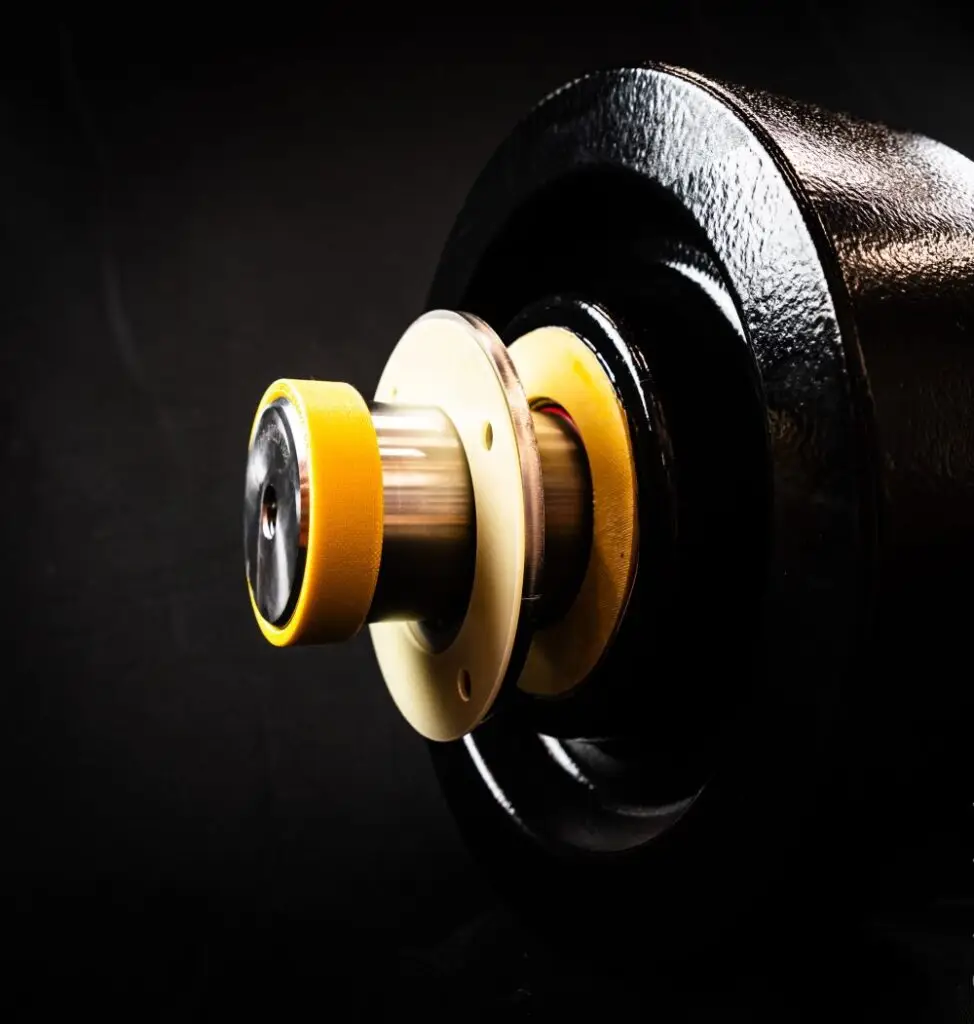
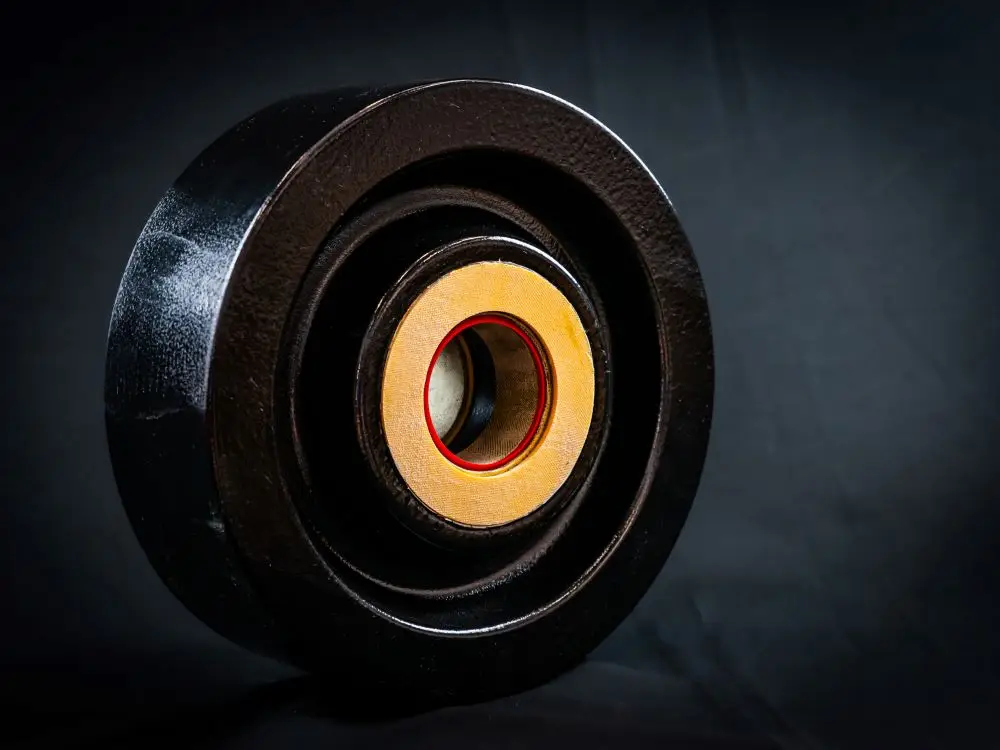
A proud contribution
Because we were already involved in the project at the design stage, it was possible to make the entire design maintenance-free and also to minimize the chance of galvanic corrosion between different materials. This means a major gain for the Grave weir in terms of reliability and expected lifetime.
At DRIE-D we are always committed to find the best possible solution for every technical challenge. If you are interested in learning how we can support you with your project, please contact us by engineer@drie-d.com or +31 10 313 4720.