D-glide® composite bearing material
What is D-glide®?
Our specially developed D-glide® composite bearing material is our flagship product, something we are very proud of.
D-glide® is a composite bearing material made from the latest generation of synthetic fibres, thermoset vinyl ester resin, solid lubricants and additives. It is a non-metallic material, offering high strength combined with a high amount of elasticity, also known as FRP or Fibre Reinforced Plastic. The resin systems have good chemical resistance, do not swell in (sea)water and are insensitive to aging. Friction modifiers such as PTFE are incorporated to minimize friction and maximize wear resistance.
DRIE-D has an experienced and enthusiastic team of engineers who develop tailor-made bearing solutions for every possible movement challenge, whereby the properties of our D-glide® composite material are used in the most optimal way.
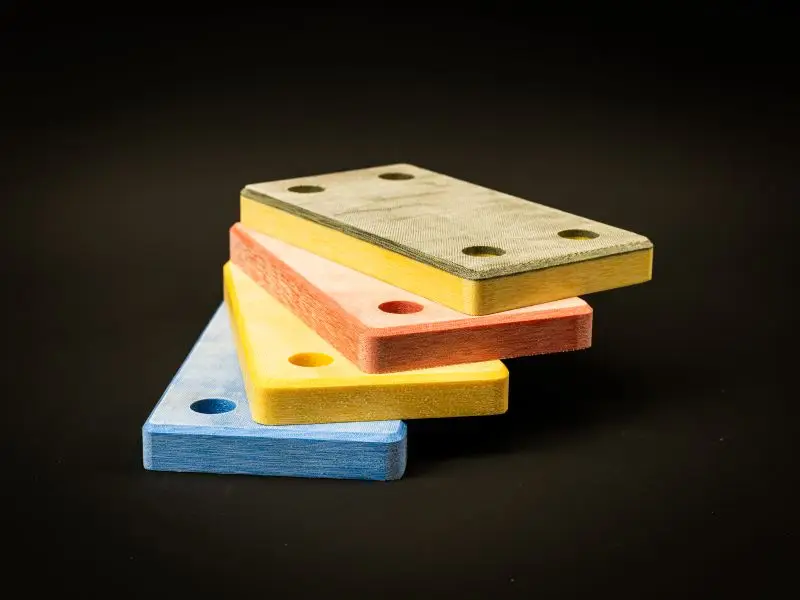
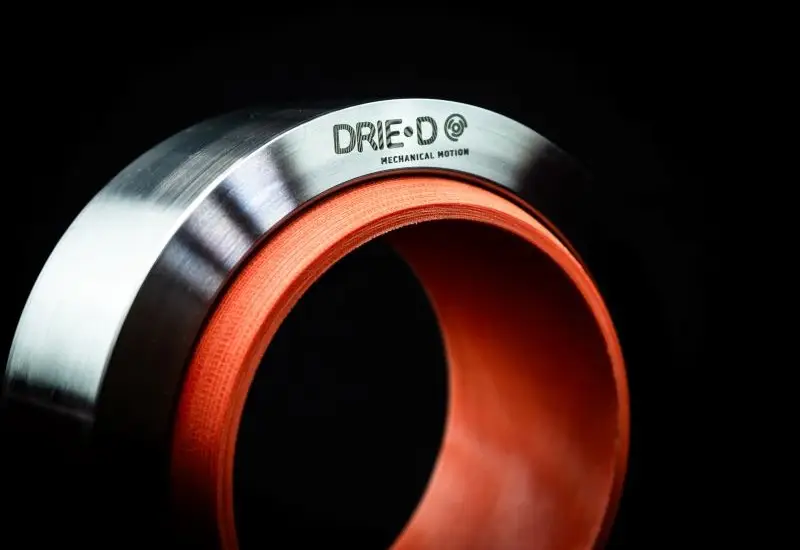
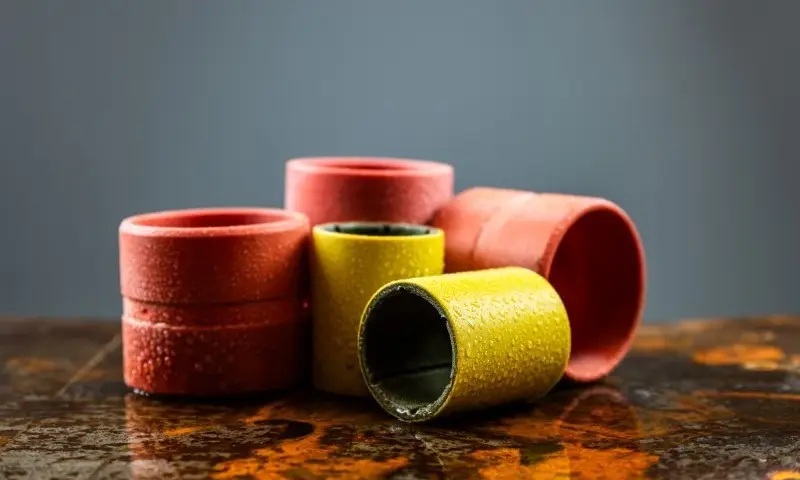
Material characteristics D-glide® composite
Unlike traditional bearing materials, such as bronze or steel, D-glide® is not a metal, but a synthetic composite material. This makes the behavior of D-glide® bearings very different, both mechanically and in terms of sliding properties.
The load capacity of D-glide® is comparable to the better metal bearings. Because D-glide® is more elastic than metals, the forces are distributed more evenly, reducing the maximum Hertzian stresses in the material. This also allows the use of D-glide® bearings in applications where large deformation or misalignment is required.
Because the material does not contain metal, D-glide® cannot corrode, cause corrosion, cannot cold weld to a mating surface, nor cause surface fatigue.
In addition, D-glide® bearings can be used maintenance-free, unlubricated. This is not only good for the environment, it also minimizes operating costs and delivers major advantages in reliability. D-glide® gets the lubrication out of its own material, so extra lubrication is not necessary and you are no longer dependent on automatic lubrication systems or the performance of set lubrication intervals.
Key features of D-glide® material
Our range of D-glide® materials sets itself apart through the key-features that are listed below.
- High-load capacity
- High Elasticity
- Maintenance-free
- Negligible water absorption
- Low friction
- Extremely wear resistance
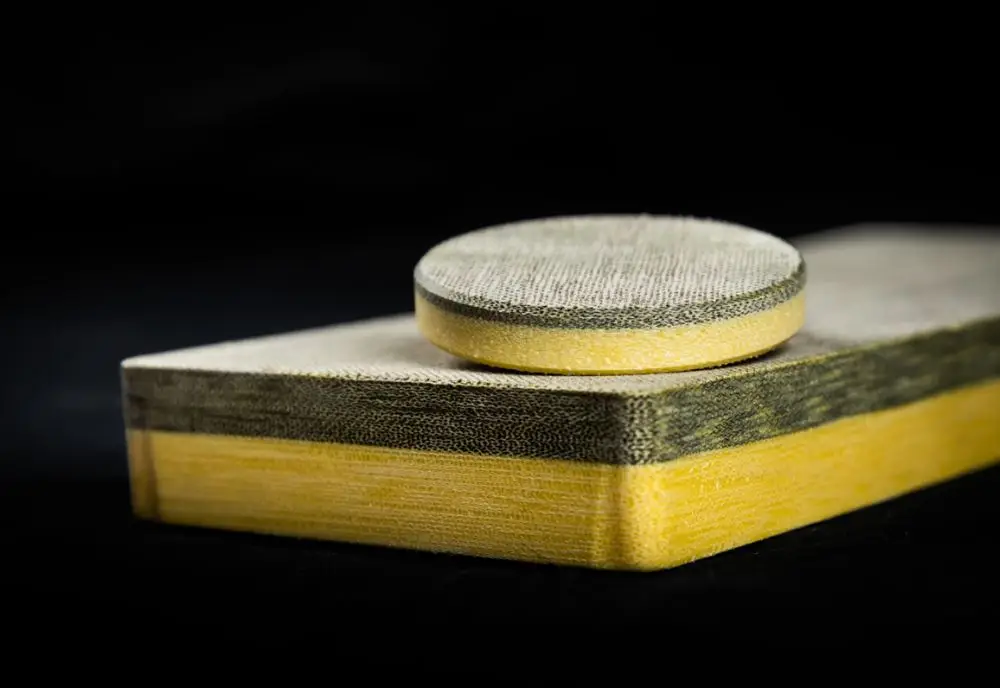
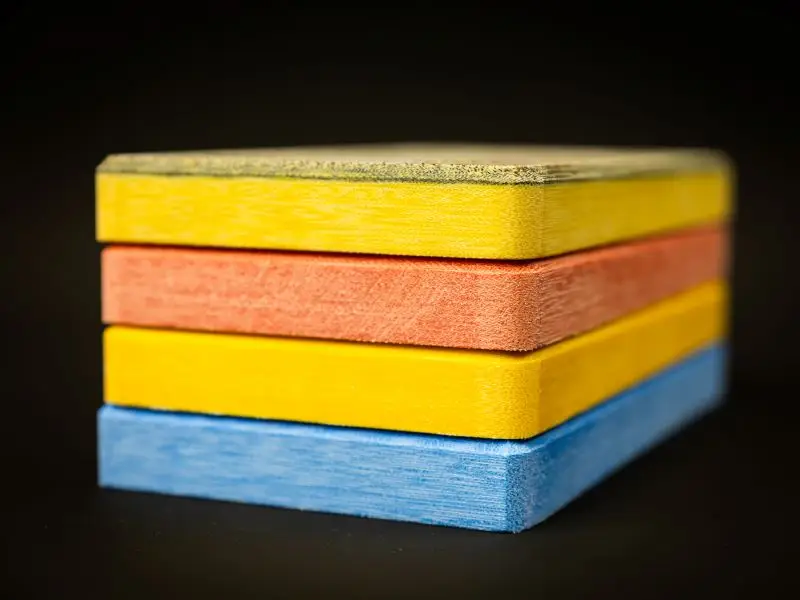
Different grades of D-glide® composite bearing material
The D-glide® product line exists out of four different grades. Each grade has its own unique properties, benefits and application limits. We want to give you a short overview of each grade.
- D-glide® F is the standard grade for all dynamic applications and an excellent maintenance free alternative for traditional steel or (self-lubricating) bronze bearings.
- D-glide® FT has a special sliding layer, which is the clearly distinguishable greenish layer. D-glide® FT has the lowest possible friction with minimal difference between static and dynamic friction.
- D-glide® FC has additional additives in the resin that increase the abrasive wear resistance of the material by up to ten times compared to D-glide® F.
- D-glide® P is suitable for all semi-static applications and an excellent maintenance free alternative for traditional steel or (self-lubricating) bronze bearings.
D-glide® products
We produce different products out of D-glide® composite bearing material for customers all over the world. Whether it is a large custom-made spherical bearing or serial produced standard parts like bushings or wear pads.
Mainly we divide our products in the following four categories:
- Spherical bearings
- Thrust washers
- Bushings
- Wear pads
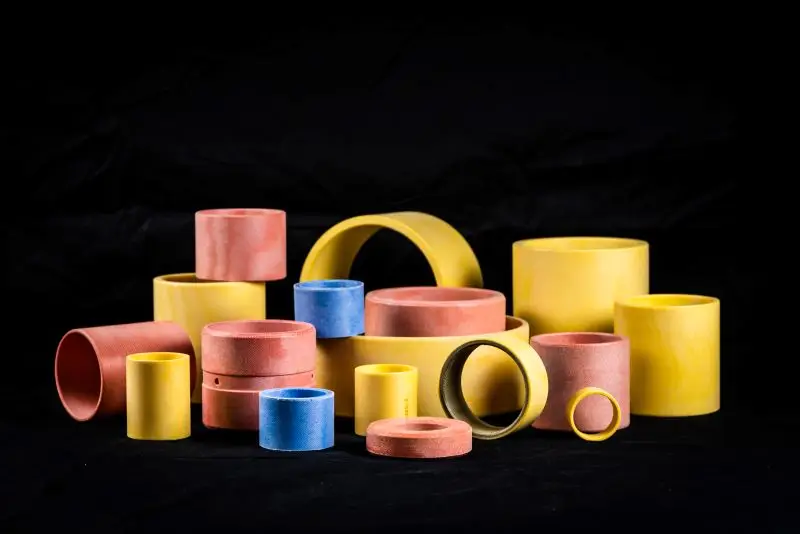
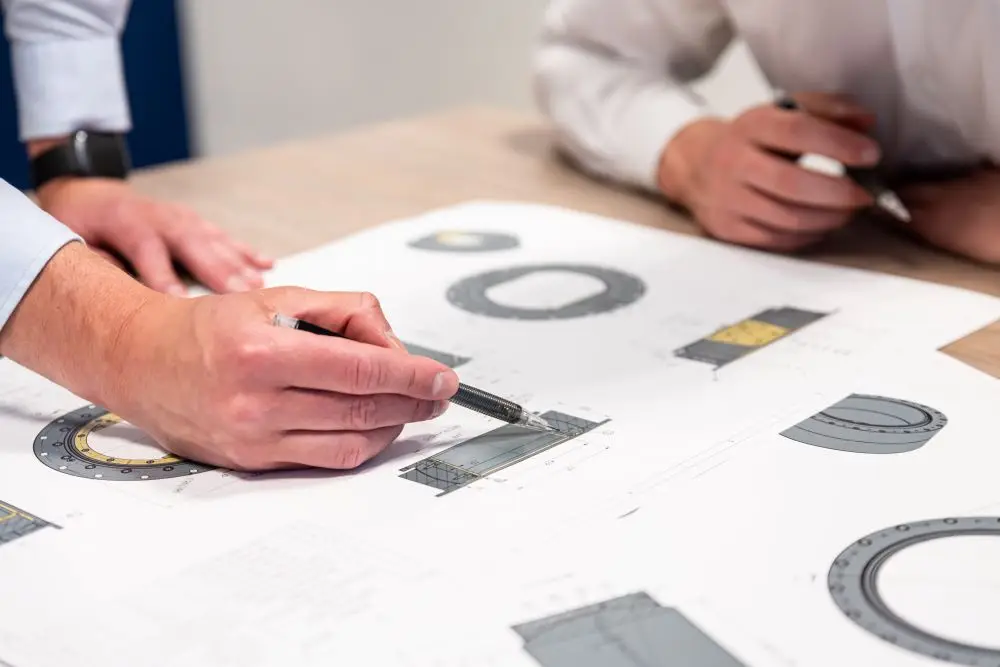
Engineering with D-glide®
Creating a bearing design from composite material requires a different approach compared to calculating with steel or bronze. In our datasheets you can find an overview of the properties of D-glide®, some values depend on the design and the way in which the material is being used.
With over 25 years of experience in engineering with D-glide®, we have built an impressive track record of challenging projects. At DRIE-D we have a dedicated in-house engineering department, continuously designing with D-glide®.
We are more than willing to share our expertise and to help you make the right choices for your bearing design.
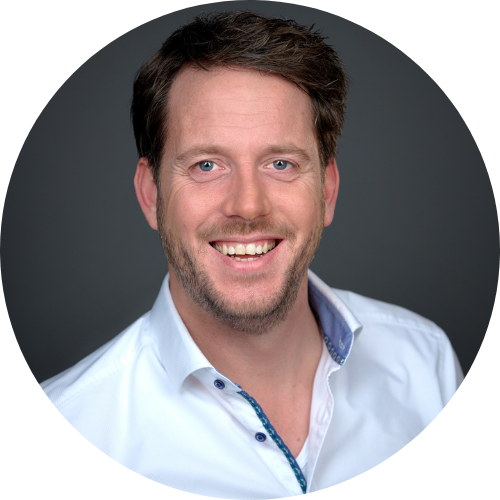
Patrick Overmeer
Product Manager
If you require a quotation or have a product-related inquiry, our Product Manager Patrick is available to assist you.
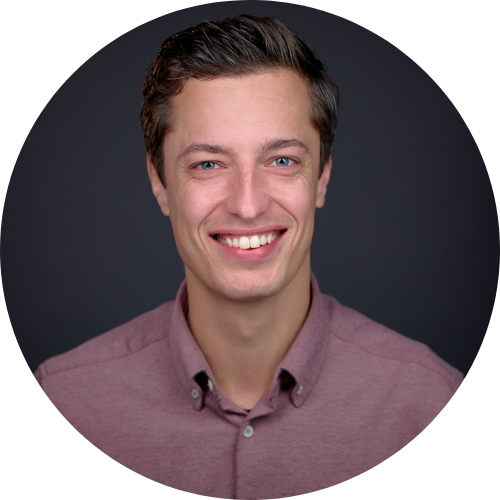
Mark Erkens
Lead Engineer
If you require technical input on your mechanical motion challenge, our Lead Engineer Mark is available to assist you.
Request the material data sheets
Fill out the contact form below to request our material data sheets. You can also indicate if you would like to get in touch with our engineering department or if you have an inquiry for which you would like to receive a proposal.
Your contact details will only be used to contact you about this request and will not be used for unsolicited sales calls.
Applications
At DRIE-D we like setting new standards for heavy loads or harsh operation, environmental safe and maintenance friendly. Highly specialized in mechanical motion, we provide a smooth solution for your rough challenge! Our engineers are experienced and specialized to design solutions in these fields.
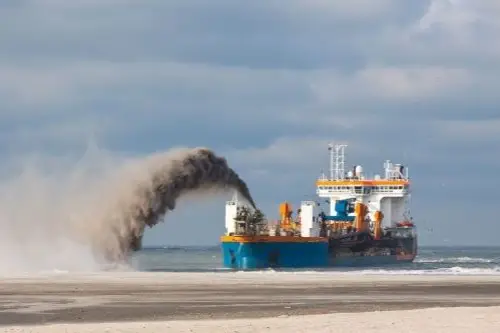
Dredging

Container handling
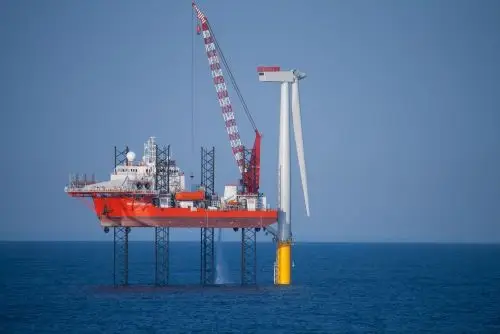
Renewable energy
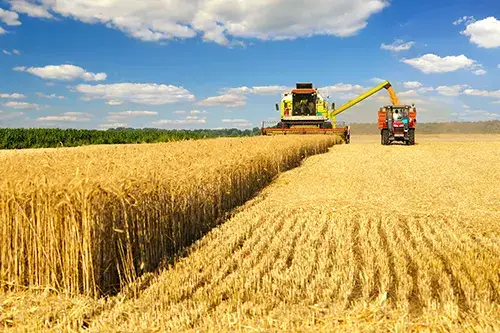
Agriculture
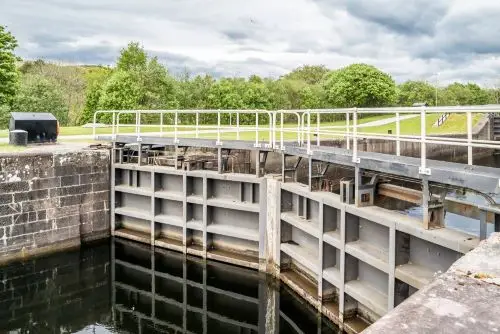
Civil engineering
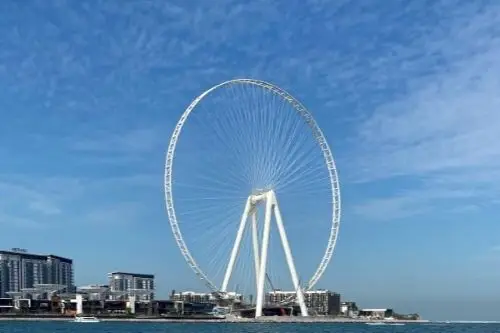
Observation wheels
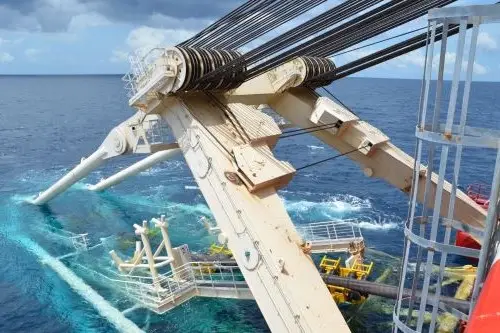
Offshore
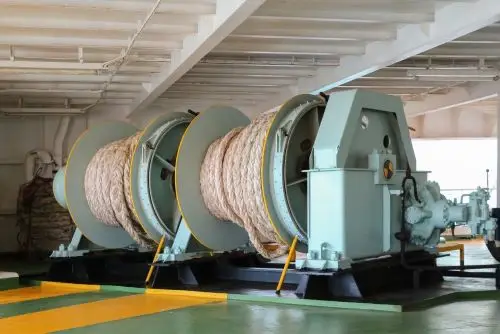
Maritime equipment
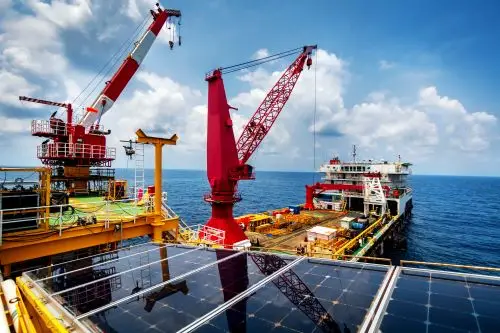
Mission equipment
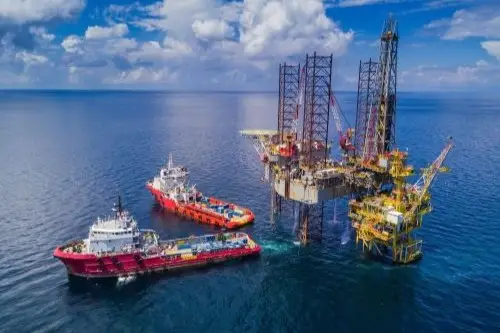
Heavy lifting

Gangways
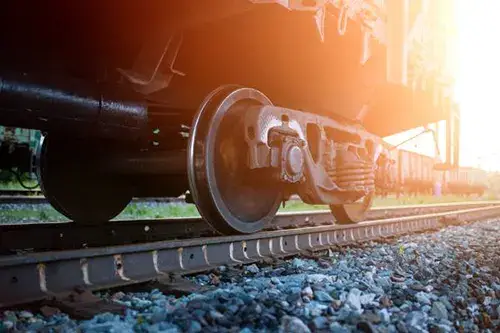
Rail
Our projects
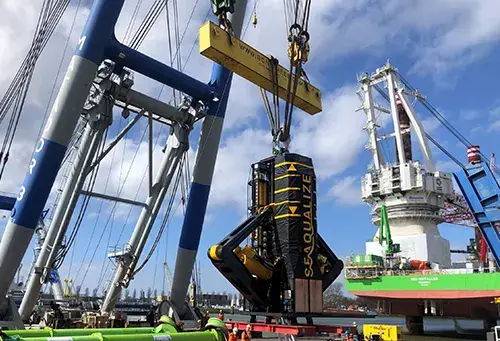
Heave Chief
Challenge: Ensuring minimal friction during continuous motion under high loads for a balanced heave compensation system.

Hexapod
Challenge: Design a lightweight solution for the limited space that is exceptional adaptable to varying angles and loads.
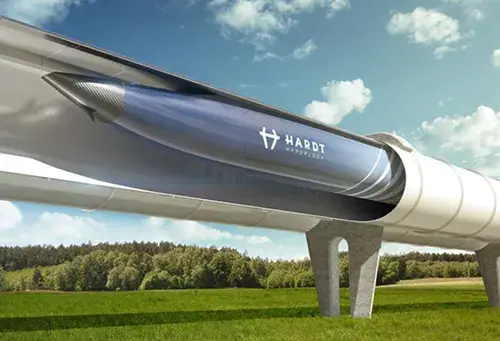
Hardt Hyperloop
Challenge: Design supports that can handle the variability in material properties, especially in relation to ambient temperature fluctuations.
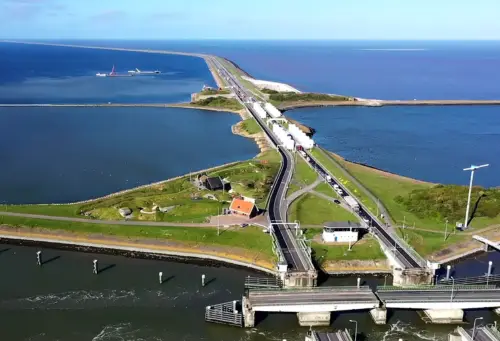
Afsluitdijk
Challenge: Design and produce D-glide® bearings for the discharge sluices, non-return valves and the innovative fish migration slider.
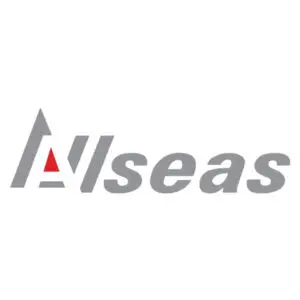

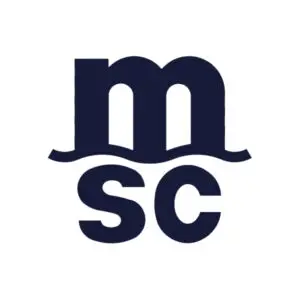
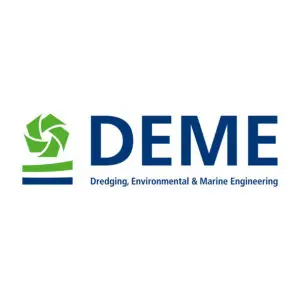
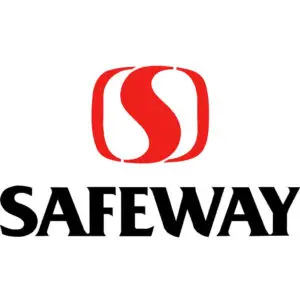
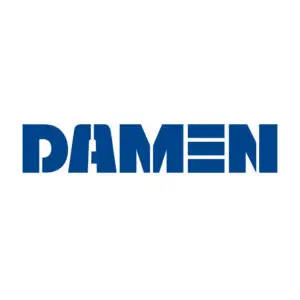
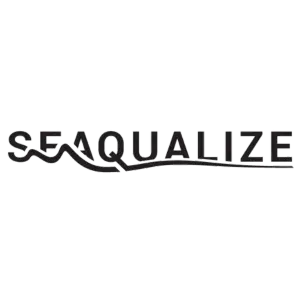
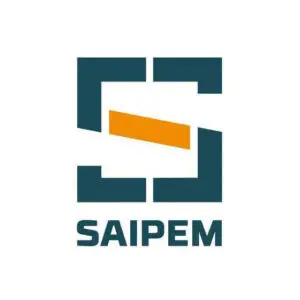

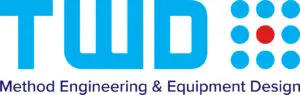

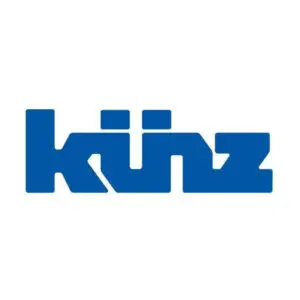
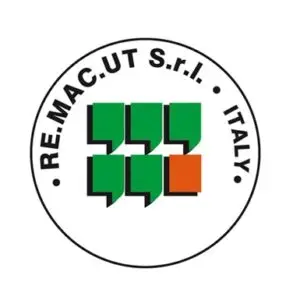
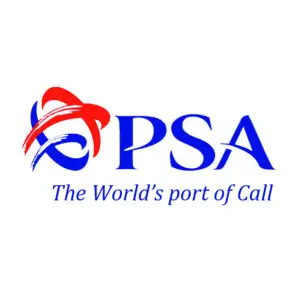
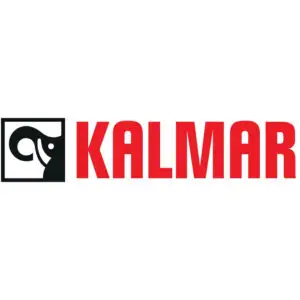

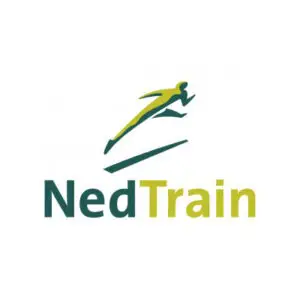

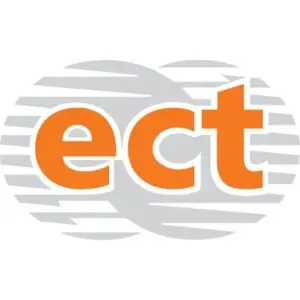

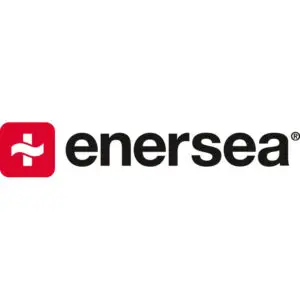
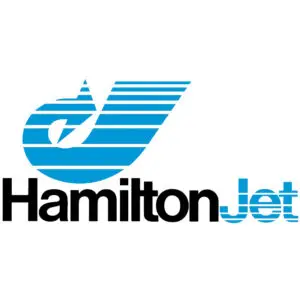
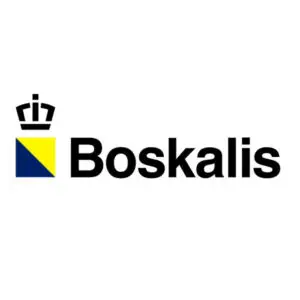
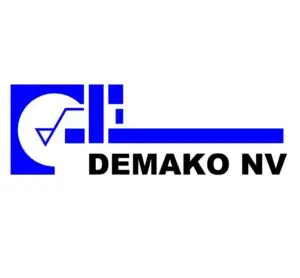
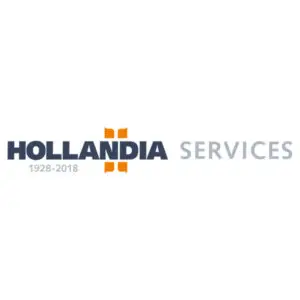

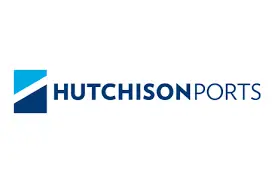
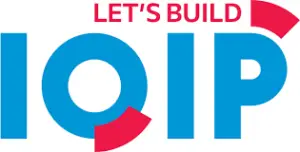
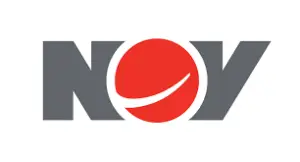
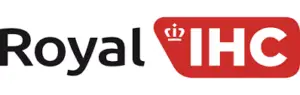
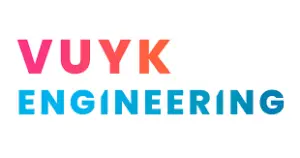


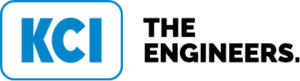
