Brake blocks
Safe and efficient braking
Brake blocks play a vital role in ensuring safe and efficient braking in machinery and equipment. These components are specifically designed to convert kinetic energy into thermal energy through friction, thereby reducing the speed or stopping the movement of a rotating or linearly moving system.
The design of brake blocks involves careful consideration of various factors, including the application’s requirements, load capacity, operating conditions, and environmental factors. The choice of material, shape, and size of the brake block is crucial to achieve optimal braking performance.
The selection of the right material for brake blocks is essential to ensure reliable and consistent braking performance. Different materials possess varying characteristics and properties that directly impact the braking efficiency and longevity of the blocks.
Common materials used for brake blocks include organic materials, such as resin-based composites, and inorganic materials, such as metallic or ceramic compounds. Each material has its advantages and is suitable for specific applications based on factors like temperature range, speed, load, and wear resistance requirements.

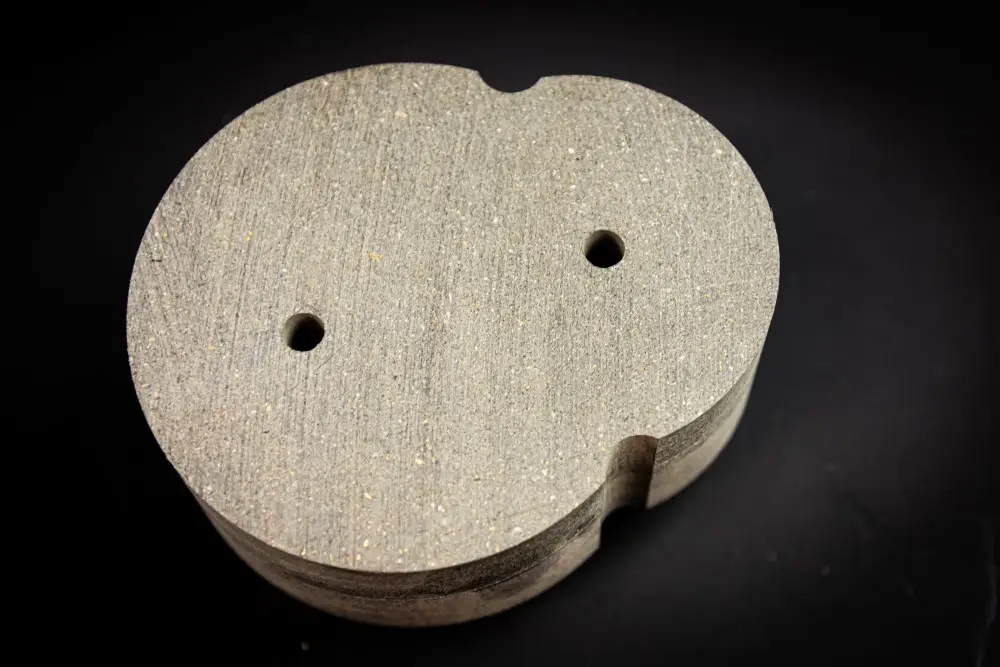
Friction and wear
Characteristics: Brake blocks must exhibit excellent friction and wear characteristics to provide consistent and reliable braking performance. The coefficient of friction (COF) is a critical parameter that determines the braking efficiency. The COF is influenced by the materials used, surface finishes, and the presence of additives or lubricants.
To enhance the wear resistance of brake blocks, manufacturers often incorporate reinforcing agents like aramid fibers, graphite, or metallic particles into the material matrix. These additives improve the block’s ability to withstand high temperatures and resist wear caused by repeated contact with the braking surface.
Performance testing and certification
To ensure the reliability and safety of brake blocks, rigorous performance testing and certification procedures are followed. These tests evaluate crucial parameters such as braking force, fade resistance, noise levels, and durability under various operating conditions.
Certification bodies and regulatory agencies set industry standards that brake blocks must meet to be considered safe and effective. The certification process involves independent testing and evaluation to verify that the brake blocks comply with these standards.


Overhaul of brake blocks
Custom made brake blocks
Custom-made brake blocks offer a tailored solution to meet specific industrial requirements and challenges. In certain applications, standard brake blocks may not fully meet the unique demands of the braking system. Customization allows for the design and production of brake blocks that are precisely engineered to address specific factors such as load capacity, operating conditions, temperature range, and braking efficiency. By collaborating closely with clients, engineers can understand the specific needs and constraints of the application and develop brake blocks that optimize performance and safety. Custom-made brake blocks may involve selecting specialized materials, incorporating specific additives or reinforcements, or modifying the shape and size to ensure a perfect fit. The advantages of custom-made brake blocks include improved braking performance, enhanced durability, increased efficiency, and reduced downtime. By investing in custom solutions, industries can achieve maximum braking effectiveness, ensuring the smooth and safe operation of their machinery and equipment. Contact us if you need custom made brake blocks for your project.
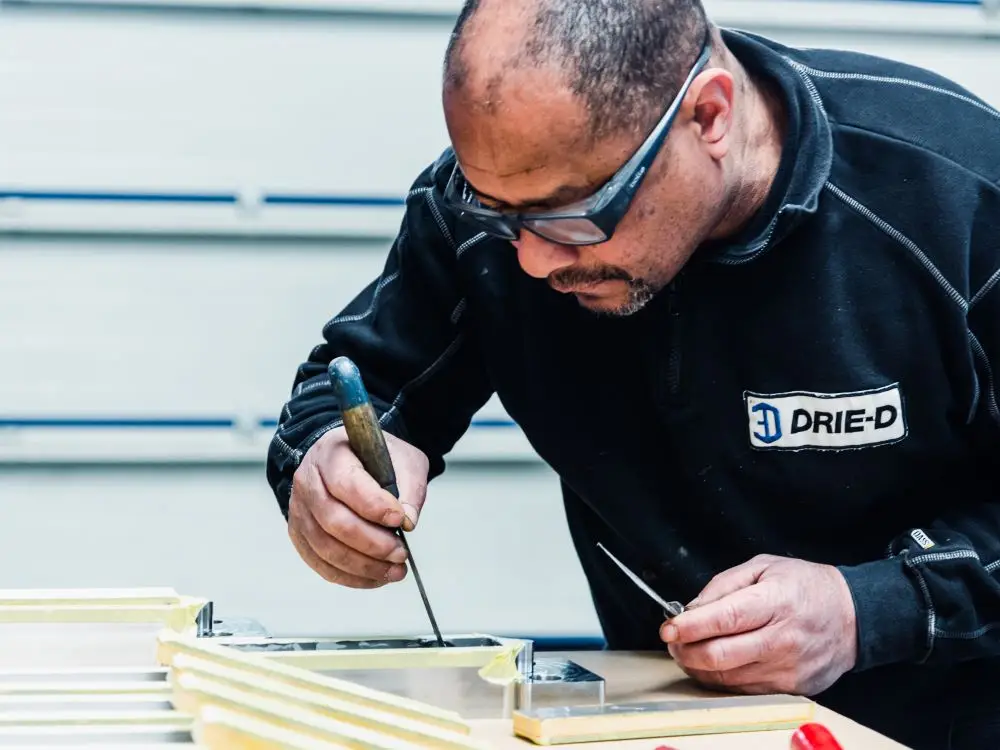

Benefits of high-quality brake blocks
Using high-quality brake blocks in your machinery and equipment offers several benefits. These include enhanced braking performance, increased safety, extended service life, reduced maintenance costs, and improved productivity. High-quality brake blocks contribute to efficient and controlled braking, minimizing the risk of accidents and downtime.
In conclusion, selecting the right brake blocks and using certified materials is crucial for ensuring reliable and safe braking in industrial applications. By understanding the technical aspects and considerations involved in brake block design and material selection, you can make informed decisions that optimize the performance and longevity of your braking systems.
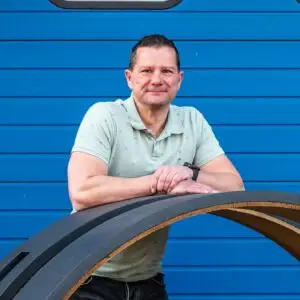
Contact us about Jurid® brake blocks
Do you need any information about Jurid® brake blocks?
Contact our Friction Specialist Dave Habets by phone at +31 – 10 3134 720 or send an email.
Applications
At DRIE-D we like setting new standards for heavy loads or harsh operation, environmental safe and maintenance friendly. Highly specialized in mechanical motion, we provide a smooth solution for your rough challenge! Our engineers are experienced and specialized to design solutions in these fields.
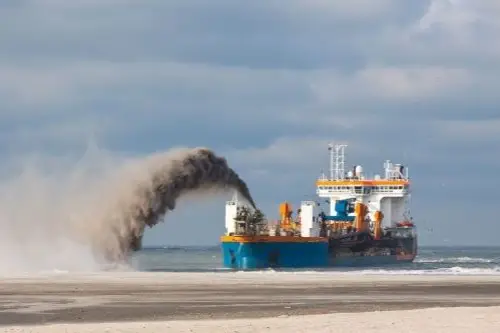
Dredging

Container handling
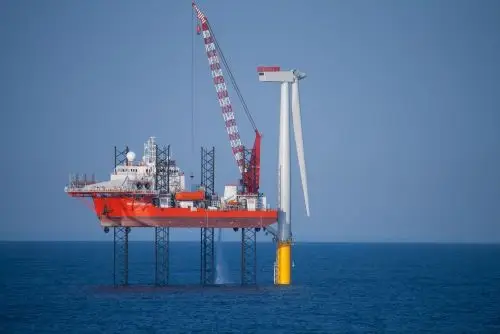
Renewable energy
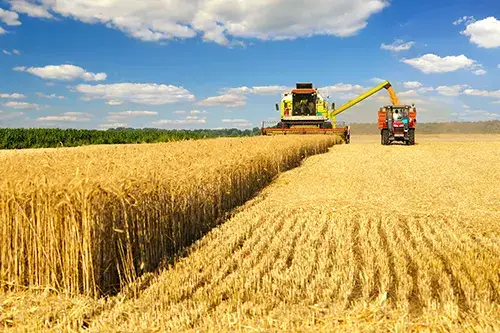
Agriculture
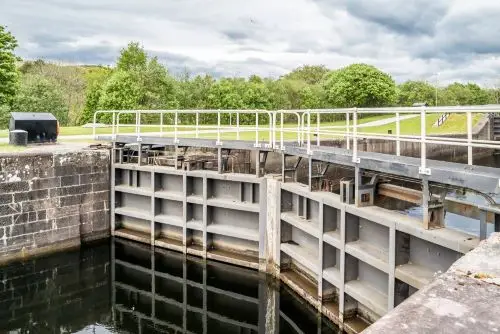
Civil engineering
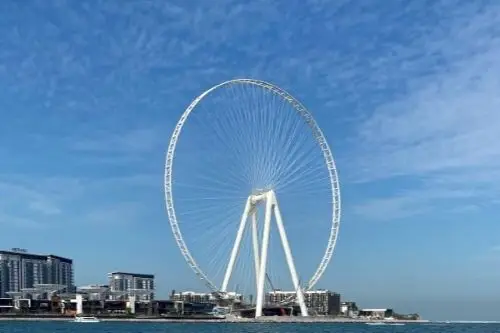
Observation wheels
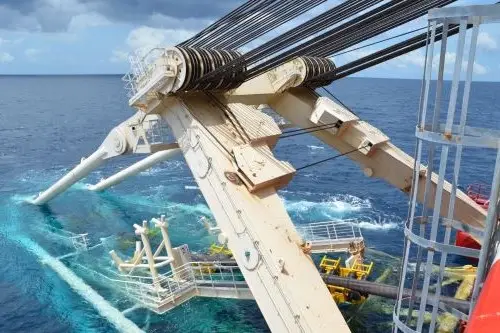
Offshore
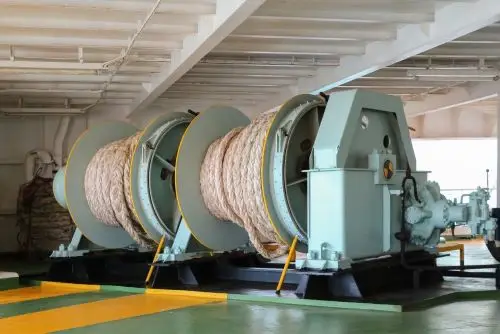
Maritime equipment
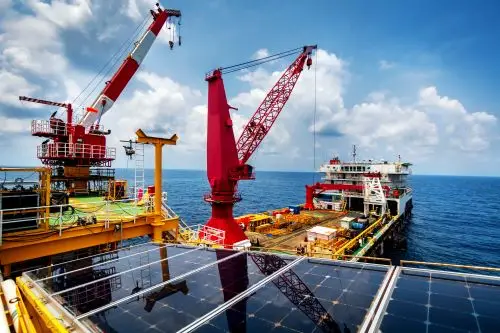
Mission equipment
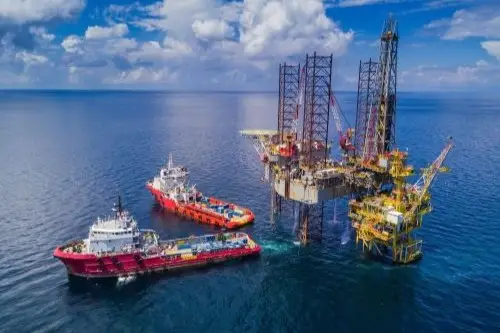
Heavy lifting

Gangways
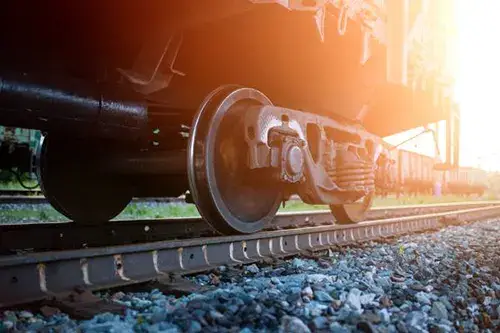
Rail
Our projects
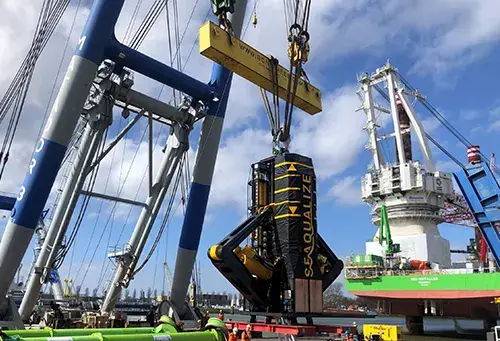
Heave Chief
Challenge: Ensuring minimal friction during continuous motion under high loads for a balanced heave compensation system.

Hexapod
Challenge: Design a lightweight solution for the limited space that is exceptional adaptable to varying angles and loads.
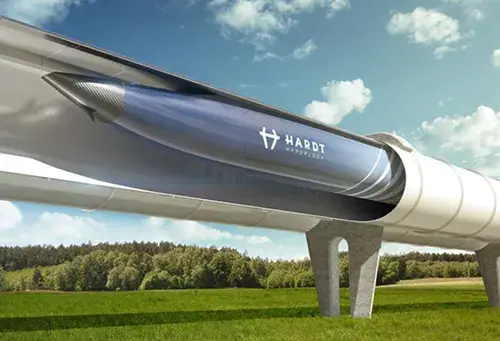
Hardt Hyperloop
Challenge: Design supports that can handle the variability in material properties, especially in relation to ambient temperature fluctuations.
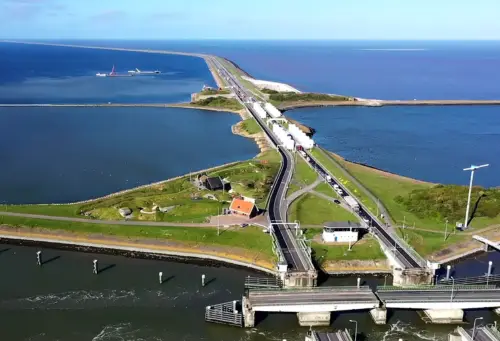
Afsluitdijk
Challenge: Design and produce D-glide® bearings for the discharge sluices, non-return valves and the innovative fish migration slider.
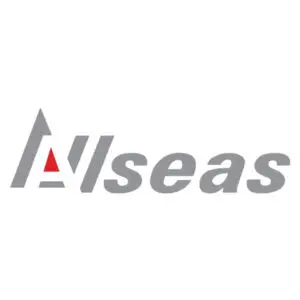

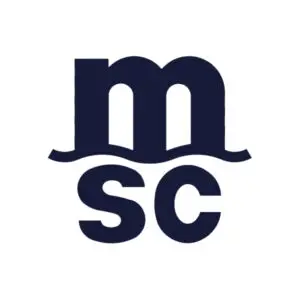
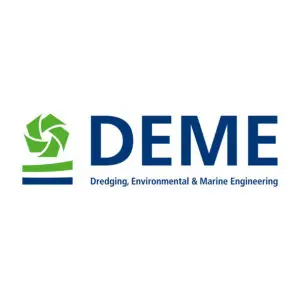
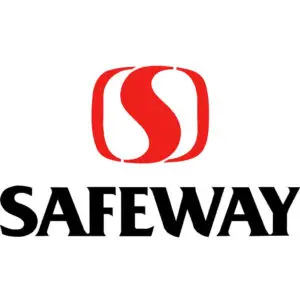
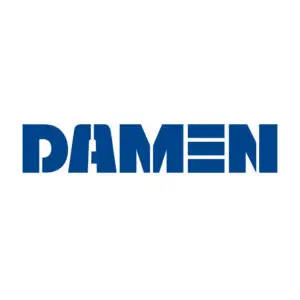
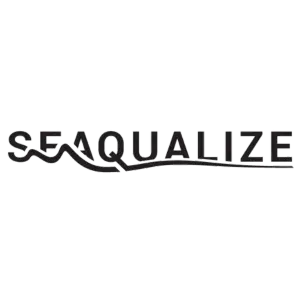
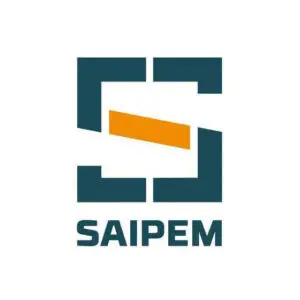

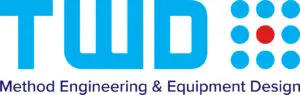

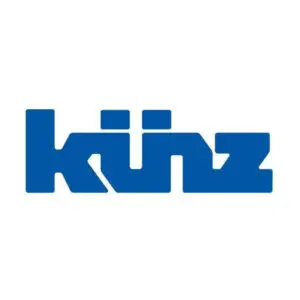
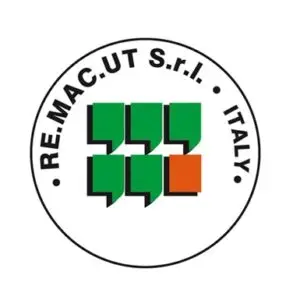
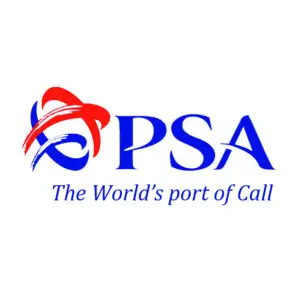
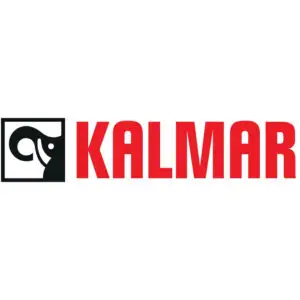

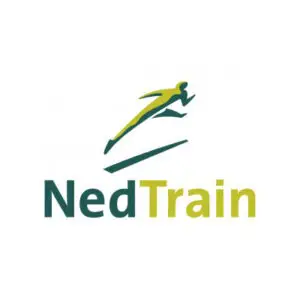

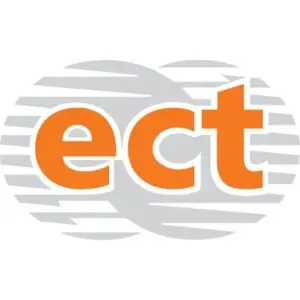

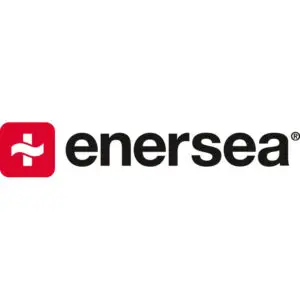
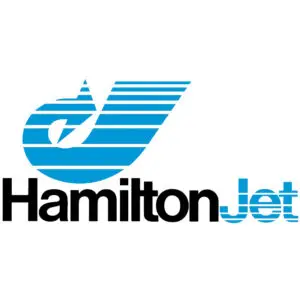
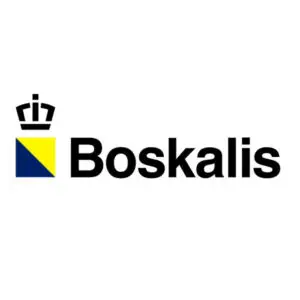
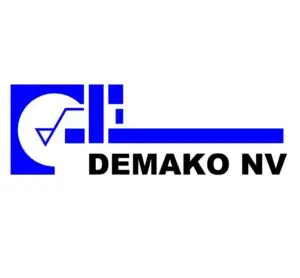
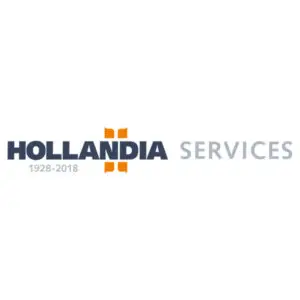

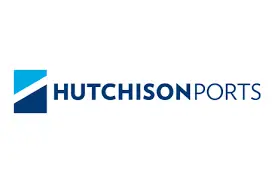
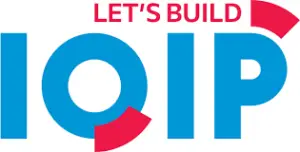
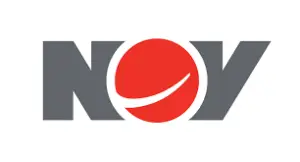
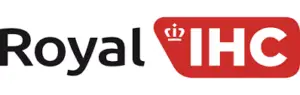
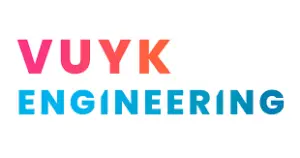


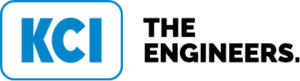
